A Pusher Oven is an industrial-grade, high-efficiency heating solution designed to meet the demanding requirements of continuous production lines. Known for its robust construction, precise temperature control, and versatility, the pusher Oven is widely used in industries such as automotive, aerospace, metallurgy, and ceramics.
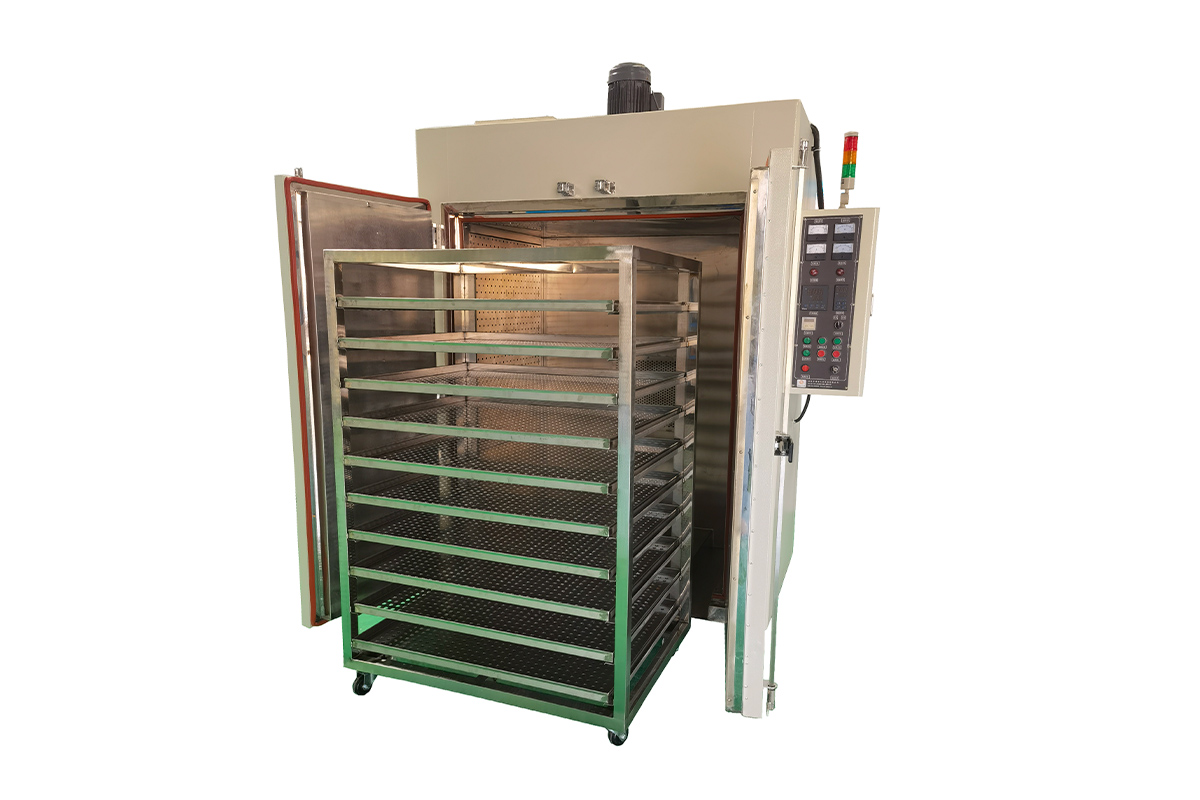
Why Choose Our Pusher Oven?
1.Continuous Operation for Maximum Productivity
Our pusher mechanism ensures non-stop material flow, minimizing downtime and keeping your production line efficient and cost-effective.
2.Custom-Built to Your Process
Tailor your Pusher Oven to match your exact needs:
Chamber size & layout
Heating zones (multi-zone control)
Material handling systems
Heating method (electric, gas, infrared)
3.Uniform & Precise Heating
Advanced heating elements and zoned temperature control deliver even heat distribution, critical for high-quality results in heat treatment, coating curing, and sintering processes.
4.Durable & Long-Lasting
Built with high-temperature alloys, reinforced insulation, and industrial-grade components, the oven is designed for continuous operation in extreme environments.
5.Energy Efficient
Lower your operational costs with:
Applications
1.Heat Treatment
Commonly used for annealing, tempering, and stress-relieving processes in the metallurgy and aerospace industries.
2.Sintering
Ideal for sintering powdered metals and ceramics, where uniform heating is critical for achieving product quality.
3.Coating Curing
Used in automotive and electronics industries for curing coatings, adhesives, and finishes.
4.Food Processing
In the food industry, pusher ovens are used for baking and drying processes, ensuring consistent results and high throughput.
Advantages
High Throughput: Continuous processing increases production efficiency.
Scalability: Customizable design allows integration into various production lines.
Quality Assurance: Uniform heating ensures consistent product quality.
Cost-Effective: Energy-efficient design reduces operational costs over time.
Who Is This For?
1.Manufacturers seeking consistent heat treatment across large volumes
2.OEMs integrating advanced thermal systems into production lines
3.Food processors requiring hygienic, uniform heat control
4.Aerospace & metalworking companies focusing on quality and repeatability