The Continuous Roller Hearth Furnace is a highly efficient industrial heating system designed for large-scale, continuous processing of materials. It features a mechanized Roller Conveyor system that transports workpieces through controlled heating zones, ensuring uniform temperature distribution and precise thermal treatment. This furnace is widely used in industries requiring high throughput and consistent product quality.
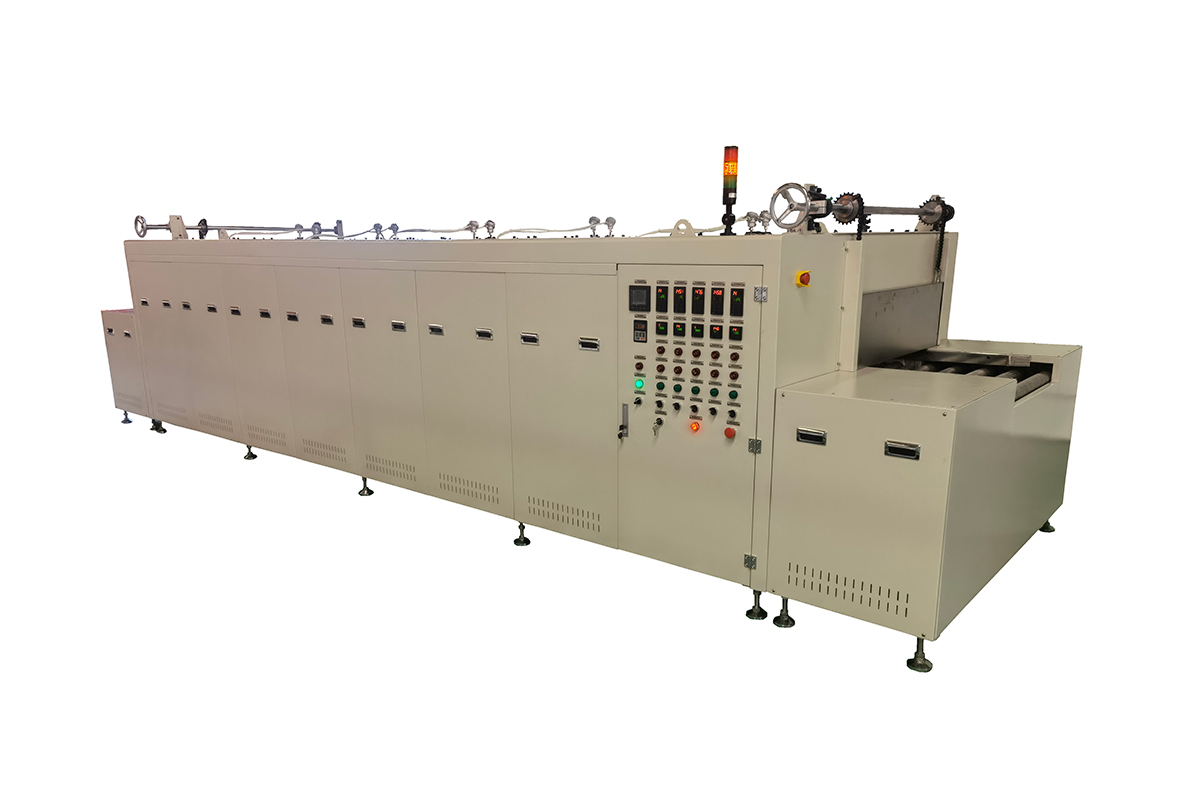
Key Features with Technical Data
1. High-Temperature Capability
Continuous Roller Hearth Furnaces can operate at temperatures ranging from 900°C to 1350°C, with some specialized models reaching up to 1600°C. The temperature uniformity is typically within ±5°C across the heating zone, ensuring consistent heat treatment results.
2. Precise Temperature Control
These furnaces utilize multi-zone PID control systems with accuracy of ±1°C. Advanced models incorporate SCADA systems for real-time monitoring and data logging, with sampling rates up to 10 readings/second.
3. Continuous Processing Capacity
The Roller Conveyor system typically operates at speeds between 0.5 to 5 meters per minute, adjustable in increments of 0.1 m/min. Standard furnace lengths range from 10 to 50 meters, with production capacities up to 2000 kg/hour depending on material density.
4. Energy Efficiency
Modern designs feature recuperative burners with thermal efficiencies up to 80%. Heat recovery systems can reduce energy consumption by 25-40% compared to conventional designs. Insulation typically uses ceramic fiber modules with thermal conductivity of 0.12 W/m·K at 1000°C.
5. Robust Construction
The roller system employs high-temperature alloy rollers (e.g., 310S stainless steel) with diameters of 50-150 mm, capable of supporting loads up to 200 kg per roller. The furnace structure is built with 6-12 mm thick steel plates for durability.
Applications
1. Automotive Industry
Used for annealing and hardening of transmission components, with typical cycle times of 2-4 hours at 850-950°C.
2. Steel Processing
For normalizing steel plates (thickness 5-50 mm) at 900-1100°C with throughput up to 15 tons/hour.
3. Glass Manufacturing
Ceramic roller hearth furnaces process glass at 600-800°C for 30-90 minutes, with specialized models handling tempered glass production.
4. Powder Metallurgy
Sintering processes operate at 1100-1300°C for 1-3 hours, with atmosphere control (N2/H2 mixtures) at ±0.5% dew point accuracy.
5. Ceramic Firing
Continuous firing of technical ceramics at 1400-1600°C with precise ramp rates of 1-5°C/minute.
Maintenance Procedures
1. Daily Maintenance
Inspect roller alignment (tolerance <0.5 mm/m)
Check burner flames (should be blue with 10-15 cm length)
Verify thermocouple readings (deviation <5°C from setpoint)
Lubricate roller bearings (high-temperature grease, NLGI Grade 2)
2. Weekly Maintenance
Clean combustion chambers (remove deposits >2 mm thickness)
Inspect refractory lining (cracks >3 mm width require repair)
Check conveyor chain tension (5-10 mm deflection at mid-span)
Verify atmosphere gas purity (99.95% minimum for protective gases)
3. Monthly Maintenance
Calibrate temperature controllers (accuracy ±1°C)
Inspect roller surfaces (wear <1 mm diameter reduction)
Test safety systems (emergency stops response <0.5 seconds)
Analyze energy consumption (compare to baseline ±5%)
4. Annual Overhaul
Replace worn rollers (typically after 18-24 months)
Rebuild burner systems (nozzle clearance 0.8-1.2 mm)
Refractory inspection (hot face erosion <15% thickness)
Electrical system testing (insulation resistance >1 MΩ)
Safety Considerations
Operate with CO detectors (alarm at 25 ppm), maintain O2 levels >19.5% in work areas, and ensure all access doors have mechanical interlocks with <1 second response time. Emergency cooling systems should reduce temperature from 1000°C to 200°C in <30 minutes.
The Continuous Roller Hearth Furnace represents a sophisticated thermal processing solution that combines high productivity with precise temperature control. Proper maintenance following manufacturer specifications ensures optimal performance and extends equipment lifespan beyond 10-15 years of continuous operation.